BIELLA SHRUNK PROCESS
since 1961, finishing first
TENSIONLESS SOLUTIONS
FOR YOUR STRETCH FABRICS
Stretch fabrics require advanced and innovative solutions, equipped with longitudinal tension control devices and feeding systems specifically designed to minimize elongation and promote longitudinal compaction.
Biella Shrunk Process offers plants equipped with technologies dedicated to this specific sector.

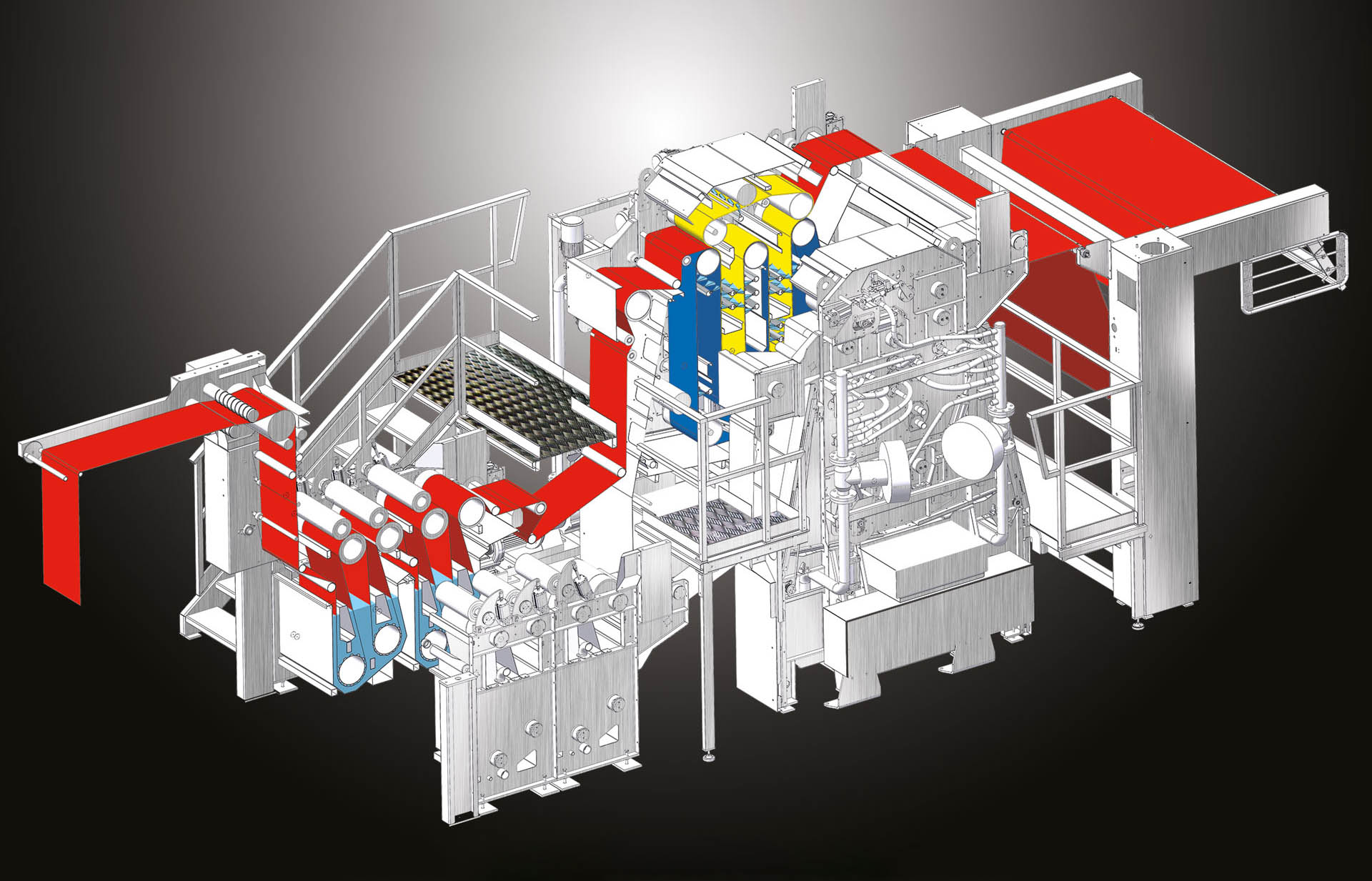
Kinetika guarantees a tensionless washing
ideal for all stretch fabrics
(natural stretch or with elastomer)
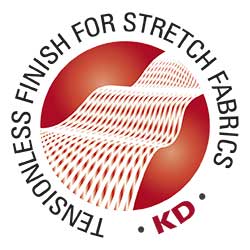
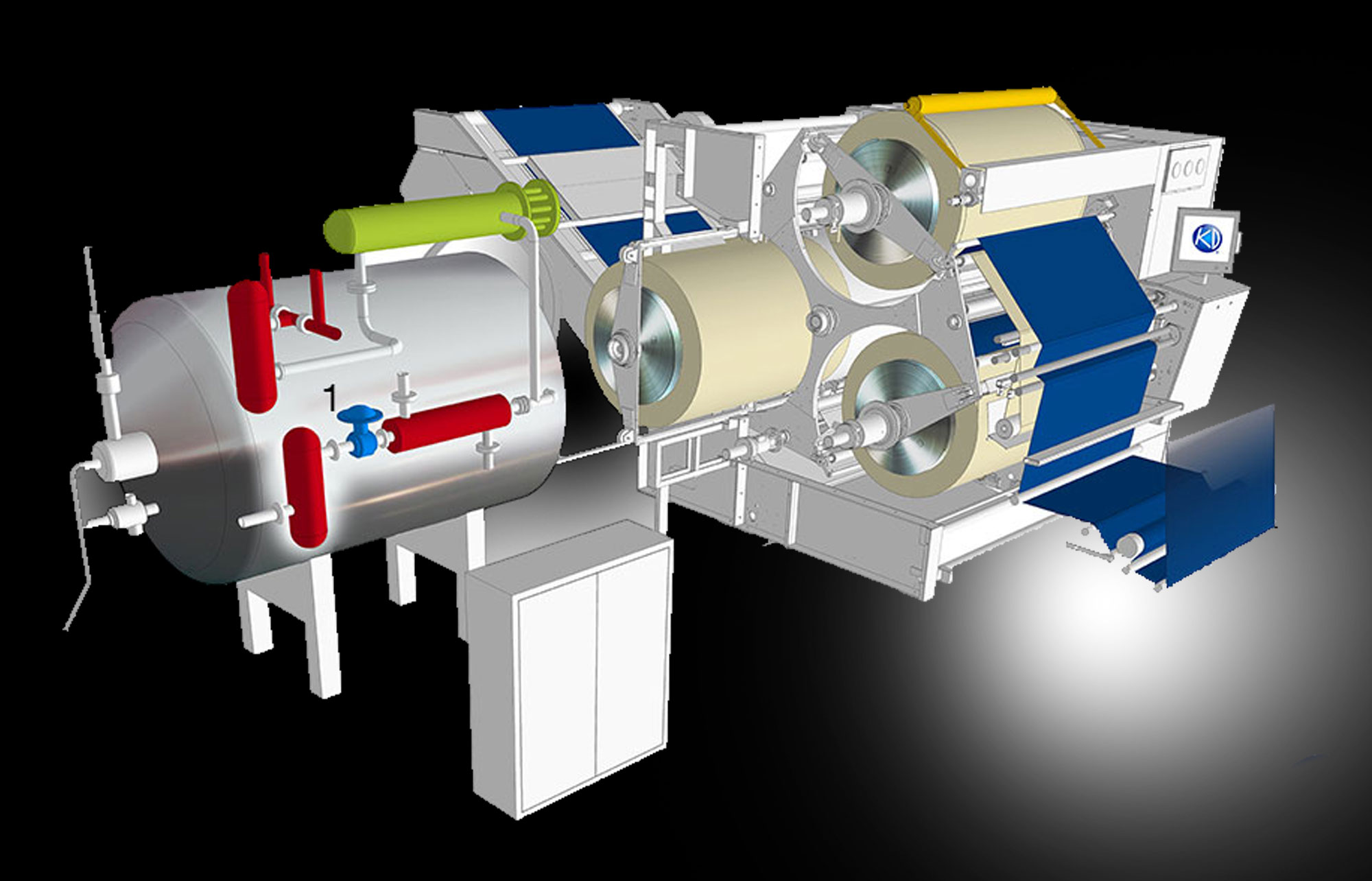
Original KD guarantees a tensionless finishing
ideal for all stretch fabrics
(natural stretch or with elastomer)
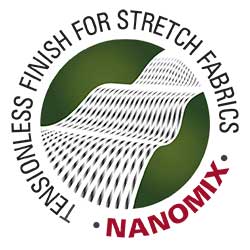

NANOMIX guarantees a tensionless finishing
ideal for all stretch fabrics
(natural stretch or with elastomer)
SINCE 1961
INNOVATIVE ATTITUDE:
THE FIRST TO DEVELOP THE ORIGINAL
KD® FINISHING PROCESS
Since 1961
INNOVATIVE ATTITUDE:
THE INTUITION OF LARGE CYLINDERS
AND THEIR EVOLUTION
CLICK AND DRAG TO SWIPE IMAGES
Since 1961
INNOVATIVE ATTITUDE:
UPDATED TECHNOLOGICAL DEVELOPMENTS
CLICK AND DRAG TO SWIPE IMAGES
Since 1961
INNOVATIVE ATTITUDE
OVER 55 YEARS OF
360° CONTINUOUS RESEARCH
Although Biella Shrunk Process and KD® represent a well established and successful combination, we have to mention some important targets achieved by our passion-driven work in the fabric finishing field.

1975 - 1978 | Autorol project (automatic – rolling):
the first ever produced fabric rolling robot, a fully automated plant able to measure, roll, cut and pack with no need of manual intervention.

1987 - 2009 | Valentina:
over 20 years of study and research in the complex dynamics behind the fabric setting process resulted in Valentina, our first continuous autoclave-decatizing machine.
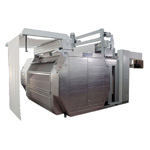
1992 | Vulco-Crab:
the continuous crabbing system based on the patented radial pressure concept, which works with an endless silicone coated belt to keep the wet fabric in contact with a steam heated drum.
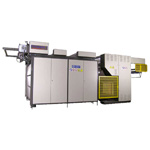
2002 | Formula 1 Multipla:
Formula 1 Multipla surprises the finishing experts with its power thanks to the double steam heated drums (patented) that offer very intense effects like “chintz” or super-finished touch
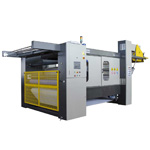
2011 | Nanomix:
the revolutionary mix of air, water and steam determined the success of Nanomix steaming and shrinking machine, appreciated for its low consumption and very intense relaxing action on the fabric.
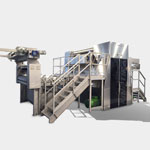
2015 | Kinetica:
the dynamic washing technology (patented) adopted by the continuous open width washing machine Kinetika: a new solution for the treatment of a wide range of fabrics.
KD Biella Shrunk Process
The Growth of Our Innovation
The Timeline of Our Innovations.
A Daring Challenge: the KD birth
Biella Shrunk Process has been founded in 1961 following a
daring challenge: create in the wool fabrics field a new finishing
process able to achieve a permanent and inalterable effect.
From this hint took origin the autoclave decatising machine,
better known with the acronym KD® (registered trade mark of Biella
Shrunk Process), which rapidly became well-known all over the world.
Smooth and soft handle, brilliant and refined look and excellent
dimensional stability are the characteristics which determined a
rapid and widespread application of such a new process which became
an internationally acknowledged quality standard.
The Automation in Rolling Technology: Autorol 75
The Autorol project is the first ever produced fabric rolling robot, fully automated plant able to measure, roll, cut and pack with no need of manual intervention, Autorol so marks the genesis of a long and fruitful series of such type of machines.
Maxima 75 the first "Jumbo" KD
The High Quality System
In 1983 has been introduced the so called "High Quality" system -patented- consisting of much larger decatising cylinders -670 mm- with differentiated perforation and oxygen-reducing internal tank. This solution allowed to increase the productivity and the treatment uniformity thanks to the reduced number of fabric layers which determined a much thinner roll to be easily crossed by the steam.
The extra-large 900 mm cylinders of KD Suprema 90
The "High Quality" patented system has been further optimized in 1990 with the KD Suprema 90 model featuring extra-large decatising cylinders of 900 mm diameter and a 1.600 mm autoclave suitable to process huge fabric lots: higher productivity and maximum versatility proven the validity of the large diameter concept.
Vulco-Crab Finishing Prabbing Plant
Based on the radial pressure rollers patent combined with an endless silicone coated belt.
KD Gigante model with 2.100 mm autoclave and two decatising cylinders of 1.500 mm diameter suitable to work with up to 4 technical fabrics
In 1999 the concept-machine KD Giant marks an amazing goal with its 1.500 mm decaitising cylinders(!) and the patented roll stocking unit which allow to use up to 4 different technical fabrics on the machine wrapper and molleton types.
Innovative Technologies
The process control technology assumes greater importance: new technical patented solutions are so introduced like the "Run-Up Cycle" using a special modulating steam reduction valve to reduce the thermal and physic shocks at the steaming cycle start-up, the "Steam Quality Control Device" which grants constant steam characteristics, or the "Combined Pressure-Tension System" suitable to obtain the ideal roll compactness.
Formula 1 Multipla
The very powerful Formula 1 Multipla surprise the finishing experts thanks to its double steam heated effect drums -patented- which allow very intense effects like the chintz or super-finished touch.
Continuous KD Machine Valentina
Over 20 years spent to study the "mechanisms" behind the fabric setting phenomenon and the analysis of continuous processes compared to traditional discontinuous technologies, these researches are then summarized in then summarized in the under pressure continuous decatising project which brings the name of Valentina machine.
KD Jubilee
The 2011 saw the introduction of a great patented innovation, which had an immediate and excellent feedback from the Customers: KD Jubilee, the first autoclave decatizing machine with integrated fabric pressing unit, which allows larger cost savings, improved quality and higher efficiency.
Nanomix
The revolutionalry mix of air, water and steam determine the success of the steaming and shrinking machine Nanomix, appreciated for its low consumption and its intense relaxing action on the fabric.
KD Futura
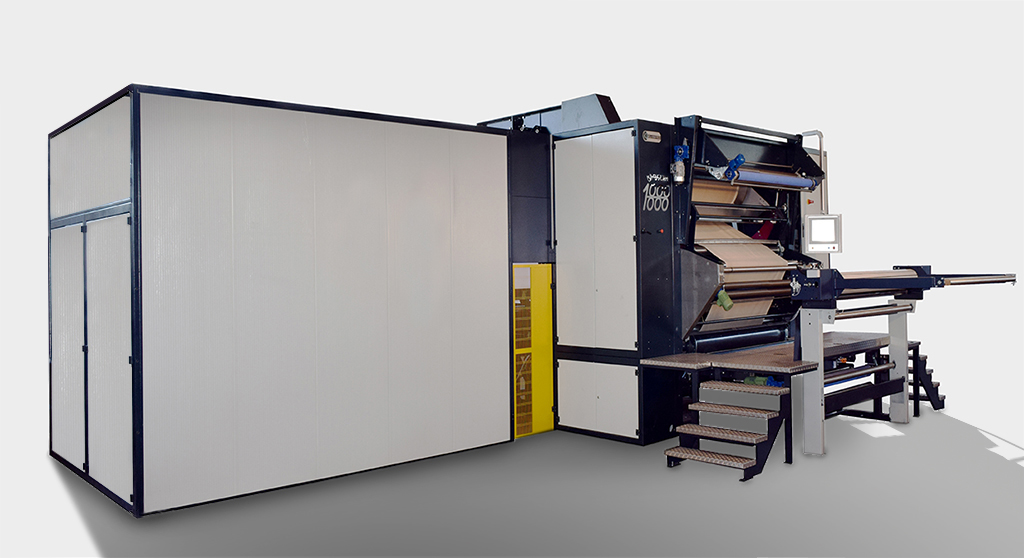
Following the success achieved by the KD Jaguar and KD Renova larger models, at ITMA 2015 was launched the KD FUTURA: a machine with large autoclave (1.888 mm) and 3 decatising cylinders of 900 mm with which it is possible to load up to 1.400 m per batch, allowing the highest productivity result.
Kinetika
The dynamic washing technology -patented- adopted by the continuous open width washing machine Kinetika introduces a new solution to treat a wide range of fabrics.
New Kinetika / Kinetika Nano / Vortex module
New washing solutions.
+39 015 92 28 80
Fax +39 015 926 286
13854 Quaregna (BI)
Italy